L'histoire du C.E.
Télécharger l'histoire du CE
1918 : La société débute la construction d'une usine sur une propriété privée de NANTES, et prend le nom de Locomotive Batignolles Châtillon (L.B.C). Dès 1919, son activité se réduit à la construction et la réparation de locomotive à vapeur.
1928 : L.B.C s'oriente vers la construction mécanique, et absorbe en 1934 la société Ernault, constructeur de machine-outil. Elle acquiert en 1935 deux sociétés de machines outils à PARIS et CHOLET. L'usine de NANTES se diversifie dans la construction :
- de matériel d'armement
- de raffinerie de pétrole
- de sidérurgie
- d'usine à papier
1943 : L'usine de NANTES est très éprouvée par les bombardements.
1950 : L.B.C amorce sa reconversion. Ses principales activités sont :
- Les raffineurs
- Les sécheurs
- Les trains onduleurs
- Les poches de coulées
- Les chariots ARMAX
- Les tourelles de chars
L'usine produit ses premiers échangeurs pour l'industrie de la chimie, des huiles et des produits pétroliers.
1956 : La société de Forges et ateliers du Creusot (S.F.A.C) prennent le contrôle de L.B.C. De nouvelles fabrications s'ajoutent :
- Compresseurs
- Mat de forage
- Pompe à boue
- Presse BLISS
1958 : Livraison des premiers Aéroréfrigérants fabriqués en France.
1970 : La S.F.A.C fusionne avec la compagnie des ateliers et forges de la Loire (C.A.F.L) et donne naissance à Creusot Loire avec comme principales fabrications :
- Les sécheurs
- Les groupes imprimantes
- Les excavateurs MATHENIN
- Les chariots ARMAX
- Les locotracteurs
- Les tracteurs forestiers LATIL
- Les échangeurs
- Les pompes
- Les aéroréfrigérants
1974 : Le secteur pompes est cédé à la société britannique WORTHINGTON BATIGNOLLES.
1984 : Dépôt de bilan qui provoque l'éclatement de l'usine de NANTES en trois groupes, avec les activités suivantes :
- WORTHINGTON (G.B) qui possède les pompes.
- ROCKWELL (U.S.A) le matériel d'imprimerie.
- GEA (ALLEMAGNE) les Aéroréfrigérants et les Echangeurs.
1985 : Création de BATIGNOLLES TECHNOLOGIES THERMIQUES, Btt filiale du groupe allemand GEA, qui reprend l'activité chaudronnerie de l'usine pour fabriquer des Echangeurs et des Aéroréfrigérants.
1988 : Abandon de la fabrication des Echangeurs pour se concentrer sur la fabrication des faisceaux d'Aéroréfrigérants et d'Aérocondenseurs.
1999 : GEA est absorbé par le groupe Allemand METALLGESELLSCHAFT (MG).
1. Présentation du site de NANTES
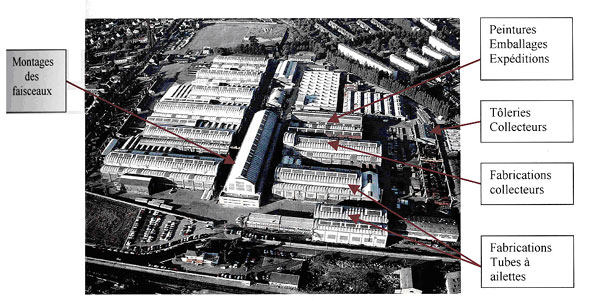
1.2 Les ateliers
Pour toutes les fabrications, l'entreprise comprend trois Unités Autonomes de Production (UAP), ces unités de production ont été mises en place en janvier 2003.
- UAP collecteurs
- UAP tubes à ailettes
- UAP montage
2. LES PRODUITS FABRIQUES ET L'EXPORTATION
2.1 les produits fabriqués
BTT fabrique deux types d'appareils ; les Aéroréfrigérants et les condenseurs.
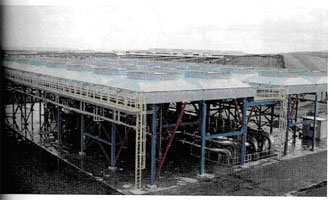 Batterie d'Aéroréfrigérants |
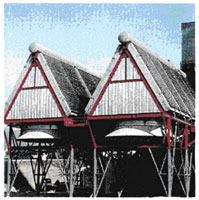 Aérocondenseurs |
L'aspect extérieur est similaire, mais la méthode de fabrication est différente en raison d'une pression très supérieure dans les Aéroréfrigérants. Le principe de ces appareils, est de refroidir un liquide ou gaz en cédant des calories au milieu extérieur.
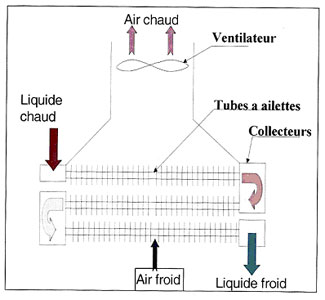
Fonctionnement d'un Aéroréfrigérant
2.2 L'exportation
Le marché dans lequel BTT s'est développé est destiné à 95 % pour l'étranger.
- MOYEN-ORIENT
- ASIE
- EUROPE
- AUTRES
Nos clients sont principalement :
- les raffineries de pétrole, les usines chimiques et pétrochimiques (SHELL, TOTAL, ESSO, ANTAR, ELF…..),
- le secteur de traitement du gaz naturel (Air Liquide, G.D.F),
- la sidérurgie : circuits de refroidissement de hauts fourneaux et de convertisseurs,
- le secteur de l'énergie (centrales thermiques ou nucléaires),
- les usines d'incinération d'ordures ménagères,
- les utilisateurs de réfrigérants de compresseurs,
- les grosses structures désirant réaliser un système de climatisation (eurotunnel).
3. LES DIFFERENTES UAP (Unités Autonomes de Productions)
La fabrication d'un faisceau d'Aéroréfrigérant ou d'Aérocondenseur se décompose en 3 étapes
1ere étape : la fabrication des collecteurs
Chaque faisceau d'Aéroréfrigérant dispose d'un collecteur d'entrée et d'un collecteur de sortie entre lesquels sont disposés les tubes à ailettes chargés de refroidir le produit qui y circule. C'est le type de produit circulant dans le faisceau (peu ou très corrosif, liquide ou gaz) qui détermine la matière utilisée pour la fabrication des collecteurs (acier carbone, inox, duplex, titane, etc.…) et la forme (collecteur à bouchons ou couvercle).
Les éléments qui composent le collecteur sont fonction du circuit du produit dans le faisceau et l'épaisseur des tôles est fonction de la pression d'utilisation de l'appareil.
Le cycle de fabrication d'un collecteur est relativement long (environ 3 semaines entre le débit et le contrôle final) et celui-ci passe par un grand nombre d'étapes de fabrication. Ces opérations sont effectuées par trois corps de métier (chaudronniers, usineurs et soudeurs), ces opérateurs sont tous des professionnels.
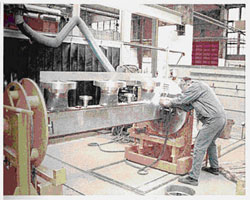 Collecteur à bouchons |
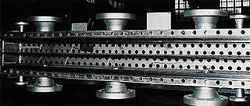 Collecteur a couvercle |
2éme étape : la fabrication des tubes
Les tubes à ailettes sont fabriqués suivant deux procédés. Le premier enroule un feuillard en aluminium autour d'un tube en acier ou métal spécial (tube enroulé), à noter que nous enroulons aussi du feuillard acier. Le deuxième procédé consiste à former par extrusion un tube lisse en aluminium, emmanché avec du jeu autour d'un tube en acier ou en matière spéciale (tube extrudé).
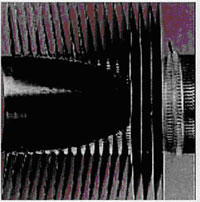 Tube enroulé |
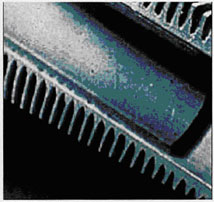 Tube extrudé |
3éme étape : le montage
L'atelier de montage assemble le châssis, les collecteurs et les tubes. Pour fixer les tubes aux collecteurs, on utilise le soudage ou le dudgeonnage*. L'ensemble est ensuite testé sous pression, peint emballé et expédié par camion.
* Dudgeonnage : opération qui consiste à réaliser une liaison mécanique, étanche entre un tube et une tôle. C'est un mode d'assemblage par expansion des tubes dans les alésages des plaques pour garantir la tenue mécanique et l'étanchéité.
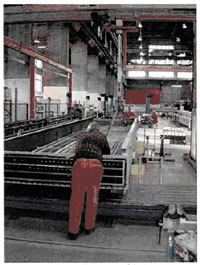
Tubage d'un faisceau d'Aéroréfrigérants
>Découvrez le site GEA BTT